New model to help valorize lignin for bio-based applications
The new model has been published in the journal Green Chemistry.
![[Translate to English:] [Translate to English:]](https://assets.w3.tue.nl/w/fileadmin/_processed_/8/d/csm_Vis%20Lignin%20Banner%20image_ec8c448ca8.jpg)
Woody biomass and wheat straw are all sources of the natural polymer lignin with more than 50 megatons of lignin produced annually at commercial scale. However, most is burned to produce energy, which alternatively could be used to make useful chemicals. A major issue with producing chemicals from lignin though is that the properties of lignin vary from source to source and from season to season. Such variability can affect the yield and quality of the chemicals produced from lignin. In a TU/e-led study, researchers have developed and tested a new and efficient model to predict the yield of lignin with specific chemical properties that are important for the production of biobased chemicals, materials, or fuels.
To date, most lignin derived from sources such as agricultural waste materials or woody biomass is burned to produce energy. As a renewable raw material, this can be seen as a waste. Researchers are looking for ways to use organic lignin as a reliable raw material for the chemical industry to make resins, foams, and biofuels.
As a source, woody biomass can be grown relatively fast, and thus it provides easy access to lignin for the long-term production of chemicals.
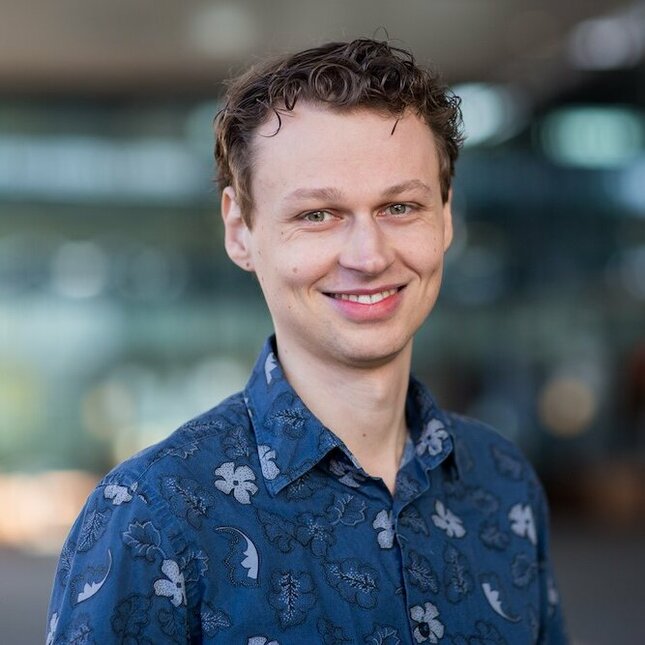
This is an idealized view of the situation though. “The major problem is that the properties of lignin are both unpredictable and variable, and this affects its usability,” says Mark Vis, assistant professor in the Department of Chemical Engineering and Chemistry and research lead of the new study published in Green Chemistry.
So, why is the unpredictability of lignin properties a bad thing? Vis explains: “Let’s say that we want to make a certain chemical using lignin, but we need lignin with a specific chemical composition to make the chemical. In any sample of lignin, there could be a million distinct types of lignin units, and isolating the right lignin type to make the chemical is the heart of the problem. Lignin does not have a single well-defined chemical structure, in contrast to the raw materials used to make conventional chemicals.”
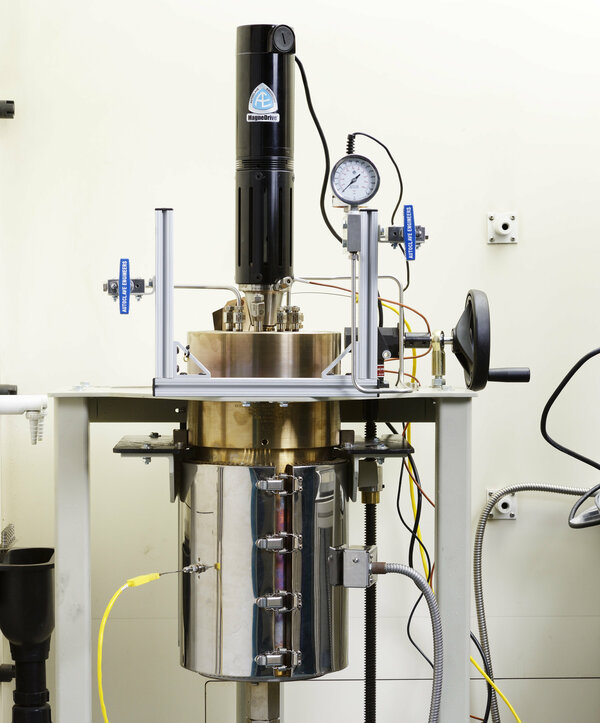
The needle in a lignin stack
This sounds like searching for the proverbial needle in a lignin stack.
A treatment process known as solvent fractionation can help isolate the desired lignin types from the stack whereby lignin types with desired chemical properties are dissolved using a solvent, which later can be purified further by removing them from the solvent.
“Fractionation can decrease the range of lignin types, but with millions of lignin types in a sample, it’s difficult to be sure that a particular solvent will isolate a particular type of lignin,” says Vis. “Theoretical calculations can help predict the outcome of fractionation, but current theories are too complex to apply to lignin. And this is the problem that we solved.”
The solution from Vis and his collaborators at TU/e (including first author Stijn van Leuken and postdoc Dannie van Osch), Maastricht University, and the spin-off Vertoro is a new model that accurately and quickly predicts the fractionation of lignin in a solvent blend containing methanol and ethyl acetate. As it turns out, a blend is better for isolating precisely the lignin fraction needed.
Model times
The researchers’ model is based on the Flory-Huggins solution theory, a famous mathematical way of quantifying polymer solubility. Usually, this model is applied to study how one polymer interacts with a solvent, but the researchers took the model a number of steps further.
“Our model is well suited if you have hundreds of different polymer types simultaneously, which means that we can model the interactions of numerous lignin polymer types with different chemical properties (such as polymer chain length and composition) with the solvent,” says Vis. “Gaining insight on these interactions is critical as they affect whether a certain lignin type will dissolve or not in a certain solvent.”
To validate the new model, the researchers calculated the fractionation of lignin derived from wheat straw and then compared the model data with experiments involving the same materials. Vis adds: “We tested our model on existing data related to a common industrial lignin in a different solvent blend (methanol and dichloromethane). Our model was applied with minimal effort, and described the data very well,” adds Vis.
To date, in terms of using numerical tools to predict lignin yields, it’s all quite speculative. “Not many people are using theory to predict yields,” says Remco Tuinier, professor in the Department of Chemical Engineering and Chemistry and also an author on the paper. “Our model makes it easy and possible to predict which lignin can be isolated with a certain solvent (mixture). It’s a significant development for the field.”
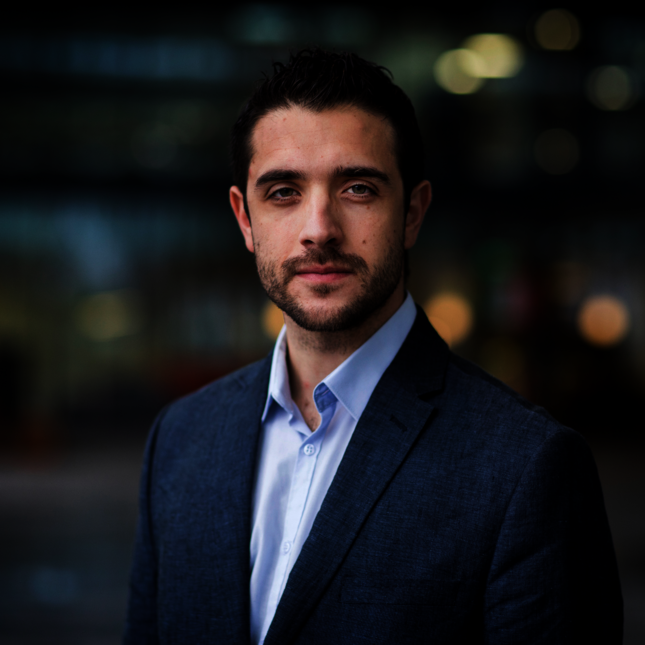
Next steps
With the model proving so successful in predicting lignin yields, how can this model make an impact in industry? Panos Kouris, Chief Technology Officer and co-founder of Vertoro and co-author of the paper: “This model is now a stepping stone for all lignin valorization activities; both in academia and industry.”
Vertoro is a spin-off company from a public-private partnership including TU/e, and wants to offer viable and affordable bio-based alternatives to fossil resources, so Kouris and his colleagues are well aware of the impact that the model can have on both academia and industry.
“In academia, the model can instigate new research lines on new solvents and lignin types, in addition to looking at ways to target particular lignin chemical properties for particular applications,” notes Kouris. “And in the biomass biorefining industry, the model could be very insightful and contribute to the design of new lignin-based products.”
Getting ready
In theory, the model can already be used by biorefineries to explore the valorization of certain lignin types, but there’s still a lot to be done before the model is ready for large-scale commercial use.
First, the model needs to be validated for the most common lignin types processed by the industry. Next, the solvent fractionation technology itself must have reached the level where the technology is ready for commercial use, and finally, clear applications of the final products are needed in the market, such as biobased packaging or biofuels.
Satisfying these requirements will take time, yet Kouris and his colleagues at Vertoro are optimistic that the model will have an impact on biorefineries sooner rather than later. “We at Vertoro expect that in the first half of 2024, the model will be extended to test several commercially available lignin sources, especially from second-generation cellulosic ethanol biorefineries that are actively looking for lignin valorization technologies and solutions.
Full paper details
‘Quantitative Prediction of the Solvent Fractionation of Lignin’, Stijn van Leuken et al, Green Chemistry, (2023).
Media contact
More on Sustainability
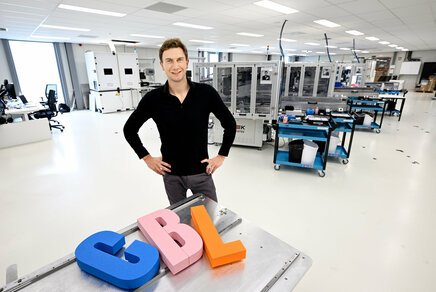
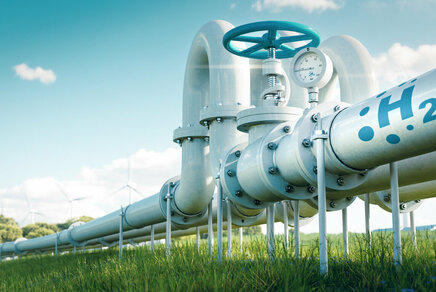
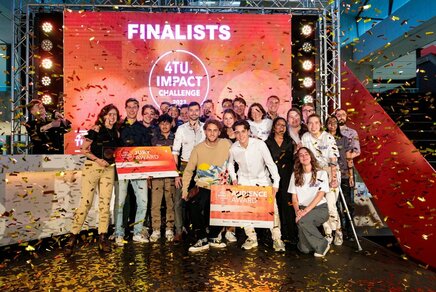
Latest news
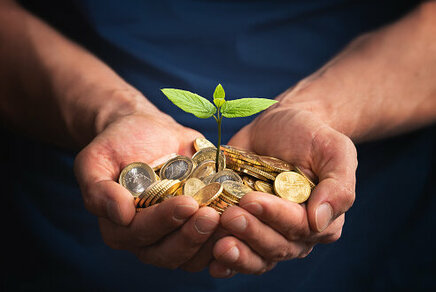
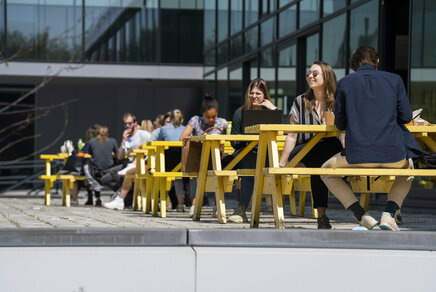
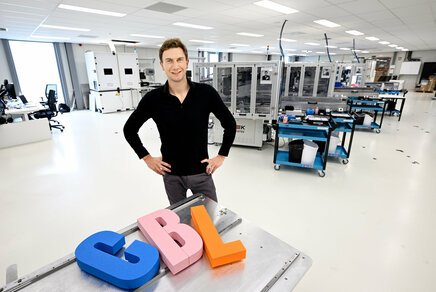