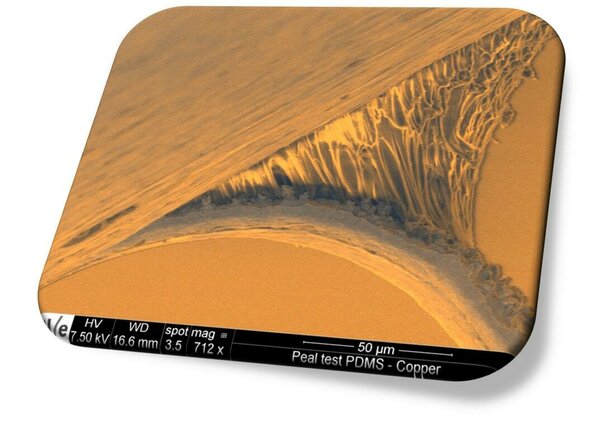
The exciting field of flexible and stretchable electronics promises numerous novel applications, particularly in-body and medical diagnostics devices, by integrating rigid functional IC components inside a flexible or stretchable matrix. From mechanical point of view, however, the huge compliance mismatch in these hybrid material systems pose new mechanical challenges, such as electrical failure resulting from the delamination and rupture of a copper interconnect line from the rubber substrate. In our research, the micro-mechanical origin underlying such failure events is investigated in detail by a combination of simultaneous electrical-mechanical testing and microscopic observation at the relevant, sub-micron scale. Integration of the gained knowledge in (finite elements) models deepens our understanding of such failures and enables device design optimization.
The exciting field of flexible and stretchable electronics promises numerous novel applications, particularly in-body and medical diagnostics devices, by integrating rigid functional IC components inside a flexible or stretchable matrix. From mechanical point of view, however, the huge compliance mismatch in these hybrid material systems pose new mechanical challenges, such as electrical failure resulting from the delamination and rupture of a copper interconnect line from the rubber substrate. In our research, the micro-mechanical origin underlying such failure events is investigated in detail by a combination of simultaneous electrical-mechanical testing and microscopic observation at the relevant, sub-micron scale. Integration of the gained knowledge in (finite elements) models deepens our understanding of such failures and enables device design optimization.