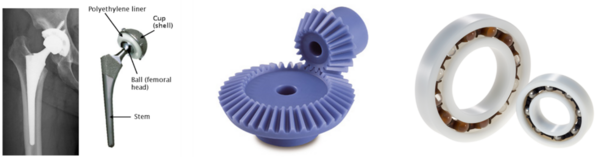
With the increasing demand for high-end (corrosion resistant, light-weight, self-lubricating, etc.) products, the application of (thermoplastic) polymers in various types of machinery becomes more important every day. In widely different types of equipment polymers play a crucial role, e.g. in bearings in automotive industry, or in medical equipment like artificial hip-joints. To increase the lifetime of, and decrease the mechanical energy loss between relative moving parts, the study of contact mechanics is crucial; in the design of such parts minimum dissipation of energy and wear rate are key factors. Whereas in metals the concept of contact mechanics, friction and contact fatigue is widely known, there are no clear guidelines for the surface design in technical polymer applications.
To speed-up the design process, accurate numerical simulations are being developed within our group, to supersede the conventional trial-and-error approach. In the recent past, combined experimental and numerical techniques have characterized the contact mechanics and contact fatigue of neat amorphous polymer systems (e.g. polycarbonate (PC) and polymethylmetacrylate (PMMA)), as well as soft and hard nano-filled systems of the before mentioned matrix material. Extending the existing analysis for amorphous materials, the aim is to use similar techniques to simulate indentation and single asperity scratch experiments in neat, semi-crystalline, unoriented and oriented polymeric systems and at a later stage, in filled semi-crystalline structures. For semi-crystalline polymers this is less straightforward as compared to amorphous systems. The main issue is the post-yielding response of these polymers.
For semi-crystalline systems the intrinsic properties are strongly dependent on crystal structure, which on its turn strongly depends on processing conditions. Hence a fundamental comprehension of both the processing/structure relation and the structure/properties relation is key. This project focusses on the influence of processing conditions (e.g. cooling rate and/or draw ratio) on the tribological properties of semi-crystalline isotactic polypropylene (i-PP), in an ultimate attempt to relate intrinsic material properties to deformation and fatigue of the polymeric contact surface (i.e. wear).
Contact
-
Lois van den Boschdr. Mick ZhouJonkerhof5171GH Stevensbeeksenn.elsenaar@ hotmail.nl
-
Isabelle de GrootMaria von Frijtag Drabbe Künzelvan der Leekboulevard3135EX Maldenkyano.huisman@ elsenaar.nl